In this article, we’ll explore the precise manufacturing process of ceramic toilets. Starting with selecting the ideal mix of materials, to shaping, glazing, and the final inspection, each step is carried out with precision and care. This ensures that every water closet we produce meets the highest standards for quality and functionality. Join us as we detail the journey of how a mixture of clay, feldspar, and silica becomes the ceramic toilets that are essential to our daily lives.
1. Raw Material Preparation
The foundation of a ceramic toilet begins with the selection of raw materials. Quality clay, chosen for its plasticity and workability, is combined with feldspar, which helps the clay become more durable once fired, and silica, which contributes to the structural integrity of the final product. These materials are carefully weighed and mixed together, creating a uniform clay body. Consistency is key, so every day, samples of this clay mixture are tested. Measurements are taken to check for uniformity in texture and moisture content, ensuring each batch meets the exacting standards required for the production of high-quality ceramic commodes.
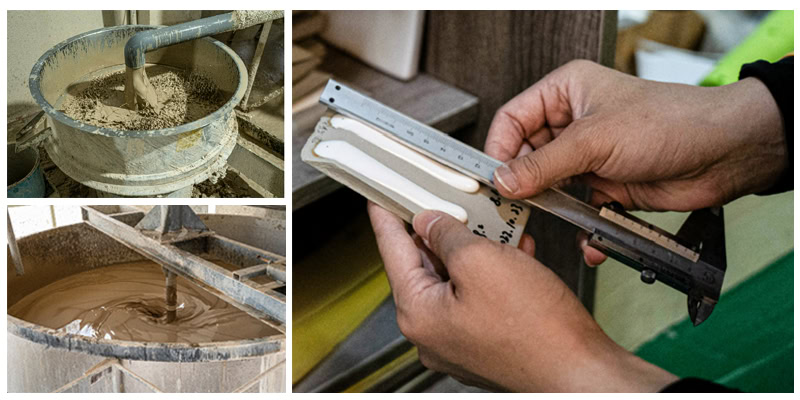
2. Casting And Shaping
The next stage in creating a ceramic water closet is casting and shaping. Here, the blended clay mixture, now a liquid known as slip, is poured into plaster molds. These molds are precisely designed to shape the toilet’s intricate contours and hollows. As the plaster absorbs water from the slip, a clay shell forms against the mold’s inner walls. When the clay body reaches the desired thickness, the remaining liquid is drained away, leaving the cast to set. After a specific curing time, the piece is carefully demolded, revealing the rough outline of a toilet, ready for the refinement that follows.
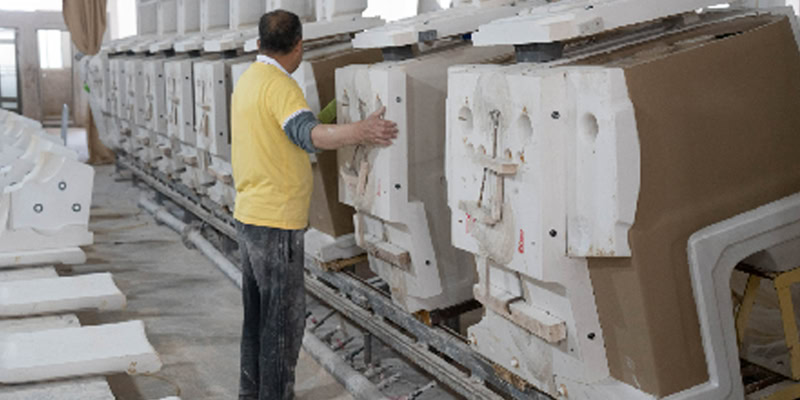
3. Fettling And Cleaning
Once the ceramic water closet forms are demolded, they enter the fettling stage where every surface is scrutinized. Skilled craftsmen remove any imperfections, refining the surface to a smooth finish with a sponge. Precise drilling creates the functional holes necessary for the toilet’s plumbing. Each piece is then measured for accurate size and levelness, ensuring uniformity across all products. The final step of this stage is cleaning the green body, where every curve and crevice is cleared of residual clay and dust, preparing it for the next phase of production.
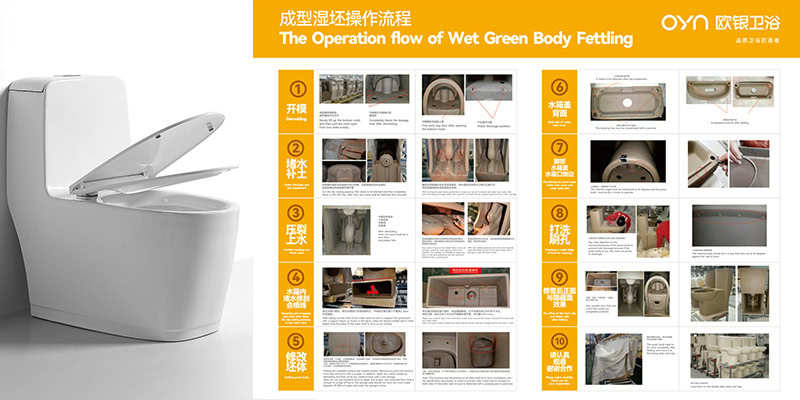
4. Checking For Cracks With Kerosene
After the fettling stage, each ceramic piece undergoes a thorough check for structural integrity using kerosene. Applied generously over the surface, kerosene seeps into any micro fissures. These potential cracks are highlighted by the kerosene’s penetration, marking areas that require reworking. This traditional and effective method ensures that each commode is thoroughly checked for durability before moving on to the next step, safeguarding the quality and reliability of the final product.
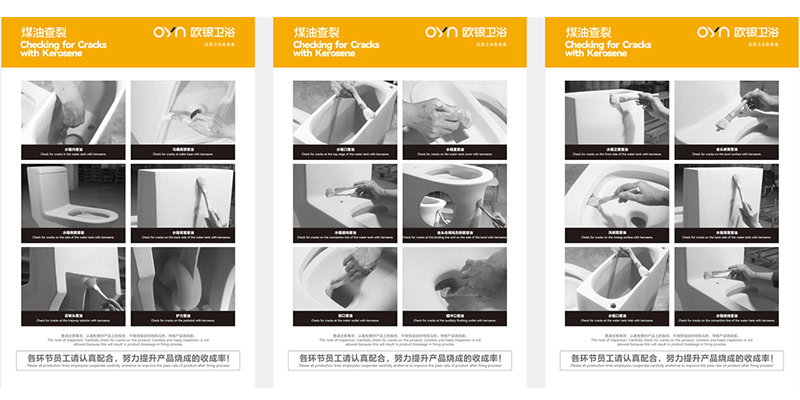
5. Drying
The drying process is conducted within a thermostatic casting hall to negate any variations in weather, ensuring a consistent and stable production environment. This controlled setting, alongside the advanced thermostatic grouting line, effectively shortens the drying time of the green body by 30% compared to conventional methods. The aim is a uniform and expedited removal of moisture, which is crucial for maintaining the integrity of the ceramic forms.
6. Glazing
During the glazing process, our glazing team applies five coats of glaze, achieving a thickness of approximately 1.1 to 1.2mm, surpassing the standard three-layer application used by most. This additional layering enhances the smoothness of the surface, effectively concealing impurities and pinholes.
Additionally, we ensure a 100% glazed trapway, which is critical for preventing clogs. By evenly glazing the interior path and firing at high temperatures, the result is a sleek surface that resists stains and is easy to clean, significantly improving the functionality of our toilets.
The final touch in this stage is the fine trimming of the water tank edge, lid edge, and toilet base, ensuring that each piece is not just functionally excellent but also visually flawless.
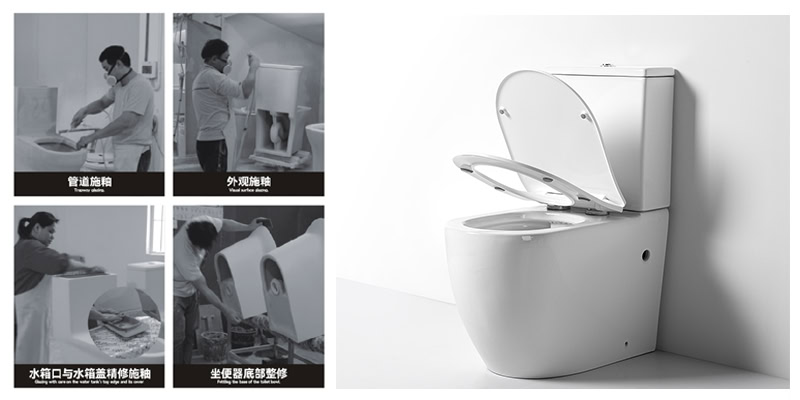
7. Kilning
The kilning stage is essential in the production of ceramic commodes, where both the body and glaze undergo vitrification. This process is achieved in an automatic controlled shuttle kiln that is designed to maintain precise temperature control, crucial for ensuring the quality of the vitrification. Our kilns operate at high temperatures, typically around 1280℃, and are capable of firing a vast array of toilet shapes and sizes. The high temperature is vital for the transformation of the clay and glaze into a hard, glossy, and durable finish that characterizes high-quality ceramic sanitary ware.
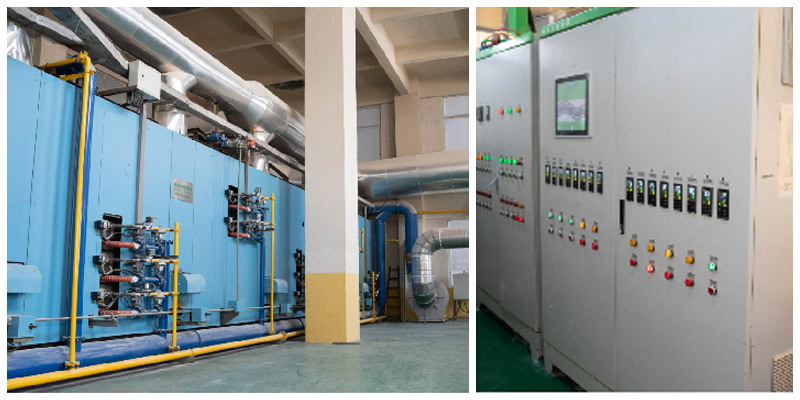
8. Quality Control
Quality control is the critical safeguard in our ceramic toilets manufacturing process. Each ceramic water closet is closely inspected for surface flaws and imperfections, ensuring that only the finest products pass our standards. We also perform comprehensive flushing function tests, using methods such as the siphon effect simulation and real-time water flow analysis to confirm flawless operation. This rigorous inspection guarantees that each toilet not only meets aesthetic standards but also operates with reliability and efficiency.

9. Packing
We prioritize the safety of our products during transit. Our approach involves robust packaging methods tailored to each item, using materials such as bubble wrap, foam, and sturdy cardboard to ensure comprehensive protection. Furthermore, we offers customized packing solutions to meet specific customer requirements, providing flexibility and personalized protection for safe transportation.
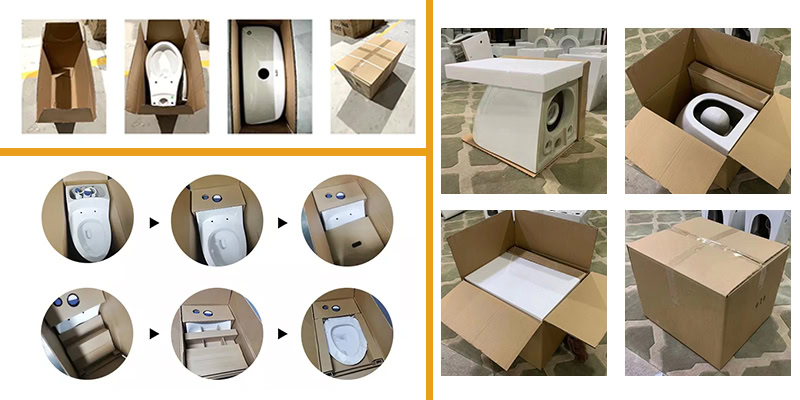
10. Loading And Shipping
The final step in our ceramic toilets production process is loading and shipping. With meticulous care, the securely packed toilets are loaded into containers, ensuring that every inch of space is utilized efficiently while maintaining the safety of the products. Once loaded, the containers are shipped to customers, completing the journey from our factory to destinations worldwide, where they will be installed and ready for use.
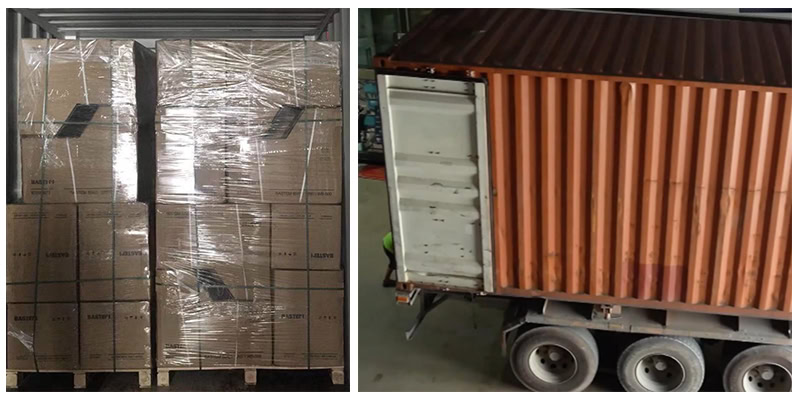
Conclusion
The creation of a ceramic toilet is a complex manufacturing process that combines traditional craftsmanship with advanced manufacturing techniques. From the initial selection of materials to the final loading for shipment, each step is meticulously executed to ensure that the final product is not only aesthetically pleasing but also reliable and durable.
As we conclude this exploration, it is clear that our dedication to crafting durable and efficient sanitary ware is what sets OYN Sanitary Ware apart in the marketplace. Our customers can trust that each piece, shaped by the hands of skilled craftsmen and cutting-edge technology, is not just a toilet but a testament to OYN’s promise of excellence in the sanitary ware industry.